Electric motors are found in practically every gadget we use daily, from cameras, phones, and fans. The mechanical energy generated by motors is used to produce a rotational motion to do work. Finding a suitable motor for a project you are undertaking can be challenging when you do not have the relevant experience.
Difference between DC, Servo, and Stepper Motors
This article will illustrate some of the critical aspects of DC, Servo, and Stepper Motors to consider when choosing a suitable motor for your project.
DC Motor

DC Motor
Direct Current (DC) Motors make continuous rotation when it is connected to a power source. DC motors are constructed using a ground wire and a power wire. DC motor will stop its rotation when a power source is disconnected. DC motors can be found in computer fans, household appliances, toys, medical devices, air ventilation systems, and radio-controlled cars.
DC motors run at high RPM, and the speed is controlled by rapidly pulsing the power on and off. The technique is referred to as pulse width modulation (PWM). The percentage of the time consumed cycling the ON/OFF ratio determines the motor rotates rate. DC Motors can be categorized into brushed and brushless DC Motors.
Brushed DC Motors
The brushed DC motor has been used in many devices from as early as the 1830s. Brushed motors are simple to construct and control, and it remains a favorite among technicians. The current in a brushed motor is connected via two metallic brushes that contact different parts of the ring. The contact, in turn, generates friction, heat, or sparks.
Advantages
- The brushed DC motor is simple to control. Connecting a voltage will drive the motor.
- Reversing the voltage will change the direction of the spin.
- They generate high torque at low speeds.
- The brushed DC motor is approximately 75-80% efficient.
- Brushed DC motors are typically inexpensive.
Limitations
- The brushes are subject to wear and tear due to continuous movement.
- There is interference to your system’s other components from audible noise generated from the rubbing parts and electromagnetic noise from sparks.
Brushless DC Motors
The brushed DC motor is a mechanically simpler device than the brushed DC motor. Commutation in the motor eliminates noise and sparks, enabling the current flow to switch silently. Therefore, the brushed DC motor is driven quietly. The rotor in brushed DC motors is more efficient than the brushes, thus eliminating any complications. Brushless DC motors find their application in electric machines that run continuously. They can be found in air conditioners, fans, washing machines, disk drives, and drones.
Advantages
- The brushless DC motor generates less electrical noise making it generally quiet.
- It is efficient than the brushed motor because it can achieve maximum rotational torque for long periods.
- The brushless DC motor is durable.
Limitations
- The brushless DC motor can be challenging to control, and you might need a specialized regulator.
Servo Motor
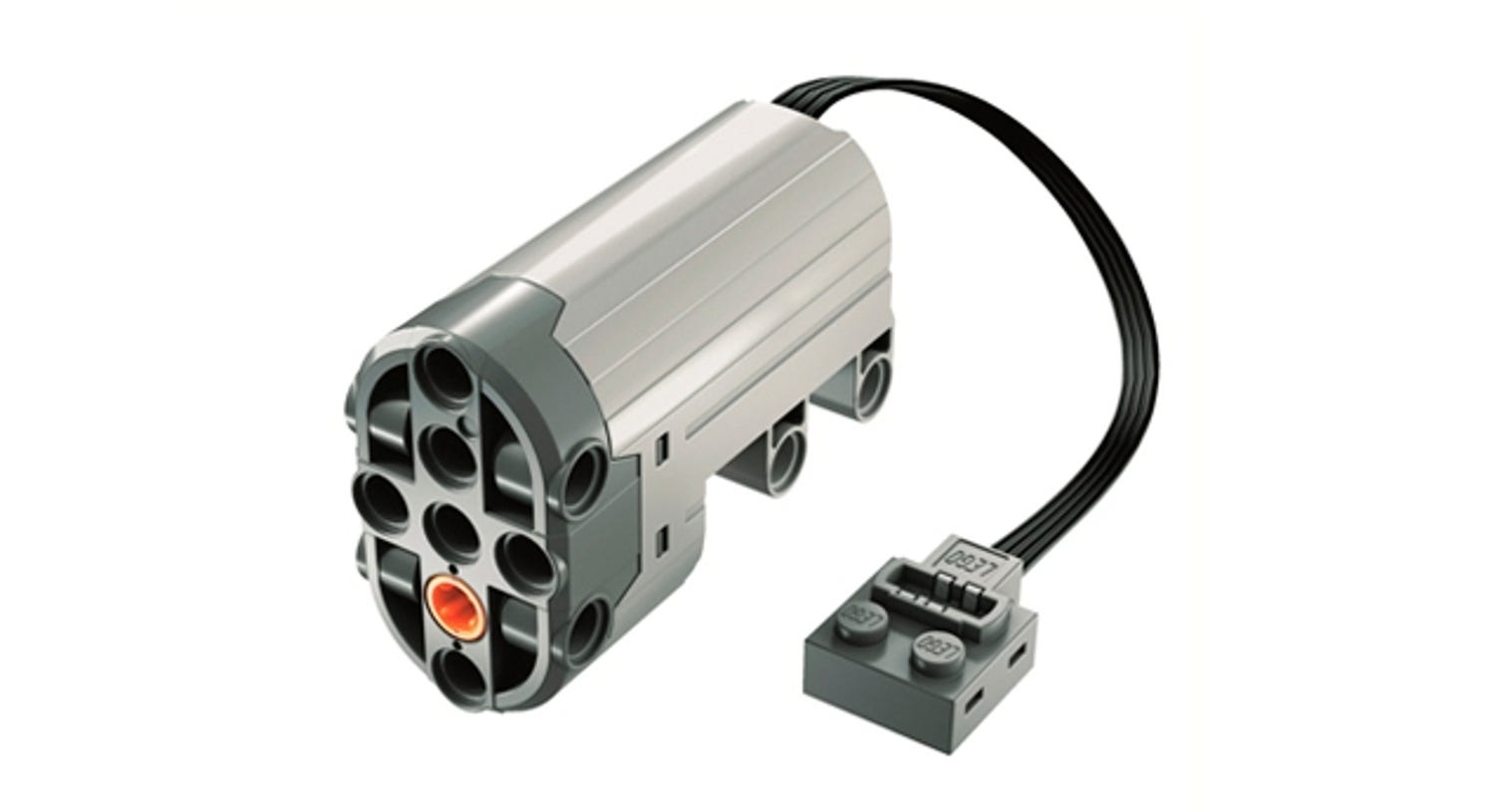
Servo Motor
The servo motor is known for its precise motion control. The servo motor is constructed from the assembly of the following components; a DC motor, gears, a potentiometer, and a control circuit. The gearing set inside a servo motor will slow down the internal high speed while increasing the torque. The positional sensor in a servo motor is fitted on the final gear. The microcontroller will determine the rotor’s current position to the desired position. The error signal generated by the microcontroller is used to move the rotor to the desired position. Servo motors can be categorized into positional rotation motor and continuous rotation motor.
The positional rotation servo motor is fitted into applications where moderate precise positioning is required. It does not provide speed control or continuous rotation. It has an inbuilt physical stop mechanism built into the gear to prevent turning beyond a 180 degrees range.
The Continuous rotation servo motor can turn continuously in a clockwise or anti-clockwise direction at varying speeds.
Advantages
- The servo motor can achieve high torque at high speeds of over 2000 rpm. It is used in machines that experience dynamic load changes at high speeds.
- They are available in different torque ratings and sizes.
- They are relatively cheap and lightweight.
Limitations
- The positional rotation servo motor has a shorter range of motion set at 180 degrees.
- The constant adjustment inside the motor might result in twitching.
Stepper Motor

Stepper Motor
Stepper motors move slowly in precise and discrete steps as compared to other motors. The precise positional control in servo motors makes it ideal for desktop printers, security cameras, and milling machines. The stepper motor has a control system that controls the amount of voltage sent to the motor. The appropriate voltage it receives will make a stepper motor move in fixed angle increments. There are notable similarities between the stepper motor and the brushless DC motor, but the stepper motor rotates in smaller steps. The stepper motor also contains a rotor that contains magnets. The coils are given a push or a pull as the polarity changes making the motor move. Alternating currents control the polarity of each ring. Cheap, readily available microcontrollers can control stepper motors. They draw maximum current, and their low top speed is due to the small steps.
Advantages
- The stepper motor has precise positioning because of the high pole count of between 50 to 100. They can move accurately between these poles without the aid of a position encoder.
- The precise steps in stepper motors make it ideal for 3D printers, X, Y Plotters, and cameras.
- Stepper motors provide precise speed control due to the discrete increments in movements.
- Stepper motors can achieve maximum torque at relatively low speeds of less than 2000 rpm.
- Stepper motors can be easily controlled using microcontrollers in Raspberry Pi boards or Arduino development boards.
Limitations
- Stepper motors generate some noise during operation and might not be ideal for machines that need to be quiet at high-speeds. Such devices might be fitted with DC motors.
- Stepper motors, in general, achieve less torque at high speeds than at low speeds.
- Stepper motors have low efficiency because they draw maximum current, and current consumption is independent of the load it has been subjected to.
- The low efficiency in stepper motors tends to make them hot.
- Stepper motors might skip some steps at high loads.
Recap
The guide has highlighted some of the fundamental factors you could consider while selecting a motor for your project. DC motors are fast and offer continuous rotation. They are used in machines and devices that need to rotate at high speeds of over 2000 rpm. They have been fitted into car wheels, drills, or fans.
Servo motors can achieve high torque at high speeds and can provide accurate rotation within narrow angles. Servo motors are ideal for projects where you require high performance. They are recommended for rudder control or robotics. Technicians use them as an alternative to stepper motors.
Stepper motors might be slow but offer precise rotation, positional control and are pretty easy to set up and control. They are ideal for 3D printers, medical imaging machinery, robotics, automotive side mirrors, and CNC milling machines.
You should also consider and pay attention to the following specifications when selecting a motor for your project; torque, velocity, voltage, and current. By understanding your project’s unique requirements and the available motors, you can confidently select the suitable motor for your application and project.
1 comment
Great article. Thanks for sharing the useful information. It’s important to know the difference between a servo motor and a stepper motor. It will save them save a lot of time in selecting between the motors.